History
A little family history, how Murph Guitars were born, the manufacturing history, and a tribute to our beloved father and grandfather, Pat Murphy.
The Story of Murph Guitars
Pat Murphy (Thomas Patrick Murphy II) was born on July 8, 1920 in Springfiled, Illinois and raised in Detroit, Michigan. As a young man, he served as a naval air force mechanic, stationed in the Philippines during WWII. When finally discharged, he worked in various occupations and industries over the next 15 years, marrying, moving cross country to California and raising a family in the process.
Pat was not musical, but his five children were. They were also actors and did television commercials, live T.V. shows, and theater plays in Los Angeles through-out the 1960's. Terry, Tim and Noreen acted in many TV commercials and shows in those years.
Pat's two oldest boys, Mike and Terry, were learning to play guitar. A friend, Jim Gurley, who had experience in the music industry, suggested that Pat consider making a new line of guitars and have his kids to help to promote them. A self-confessed 'Jack of all trades', Pat and family embarked on a bold entrepreneurial enterprise - to build a high-quality American made guitar aimed at teenagers and professionals and designed to rival the more expensive American made instruments.
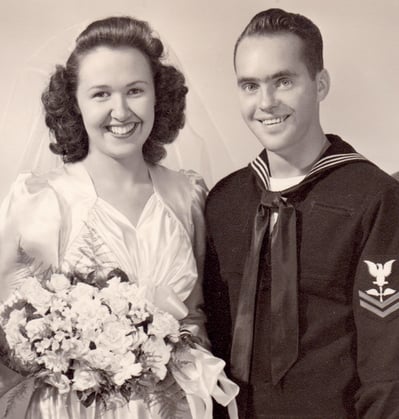
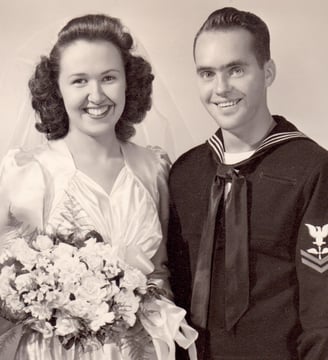
At that time, the rock and roll era was exploding. It seemed as though every teenager wanted a guitar or was in a garage band. Pat's kids were also interested in this new revolution. Mike played in bands with high school and college friends. Terry and Tim started The Murphy Jr.'s with neighborhood friends. The boys, along with their sisters, Patty and Noreen, continued their singing and dancing act as The Murphy’s, (who were similar to the Osmond's or the Jackson 5 of their time) which included live stage and television performances, as well as a recording session.
To supply this new guitar craze many new U.S. companies began building guitars. Soon, seemingly everyone from record companies like Decca, to department stores like Sears & Montgomery Ward began selling guitars under their own brand names.
Soon, the American market was flooded with imported Japanese made guitars like Yamaha, Goya, Teisco & Kawai. With all of these local & overseas companies trying to either maintain or gain a share of the guitar sales market, the competition was fierce when Murphy Music Industries started into business.
In February 1965, Murphy Music Industries commenced operations in a 1200 square foot leased building located at 1817 First Street in the industrial area of San Fernando, California. The building was modified to include a main reception/office area, a woodworking shop/sanding area, a separate paint booth, and a final assembly/inspection/shipping room- a lot squeezed into a moderate space. The building is still there today and the outside of the building has not
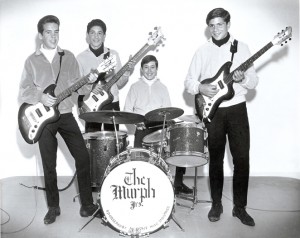
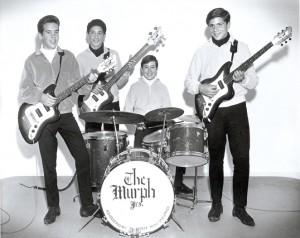
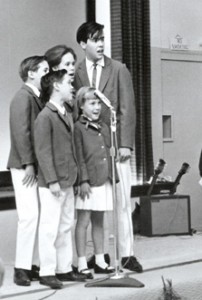
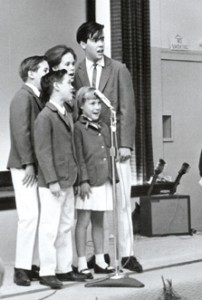
Thomas "Patrick" and Mary Jane Murphy
on their wedding day.
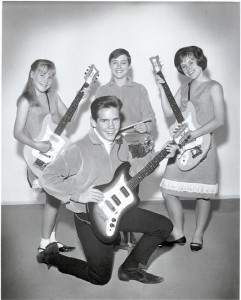
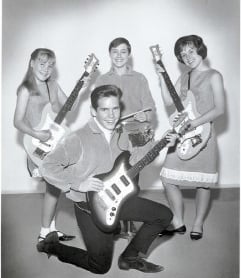
The Murphy Children in birth order:
Mike, Patty, Terry, Tim, and Noreen
changed much since then. It's been many things since it was Murphy Music Industries... in fact, from 2013 to 2018 it was once again a guitar factory when Thorn Custom Guitars began manufacturing guitars in the old Murph building.
A local engineer, Rick Geiger, was employed to set up and run the production facility. He had a lot of experience as an expert builder of stringed instruments (his father was a violin maker) and brought those skills with him to Murph Guitars.
Most of the woodworking machinery was picked up by Pat and Rick at auctions, including planers, a pin router, shaper, band saw, belt sanders and a massive drum sander. Other equipment purchased were a fret cutting machine (affectionately called a gang-groover", along with many other more specialized machines such as a coil winder for the pickups, which were encased in locally made plastic covers.
To get production started, Rick began creating the process by which all Murph Guitars would be made. Each step needed a jig or fixture to hold the guitar body or neck while cutting, drilling or routing them. After that, there was a lot of hand shaping, gluing and sanding to be done. Each phase involved many steps, from the woodworking to the painting (10 coats) all the way to the final assembly. Each step was planned carefully to minimize the amount of labor involved.
The Murph Jrs. Band
Terry Murphy left, Tim Murphy on drums, two friends of the Murphy boys.
Raw materials such as poplar for the bodies and maple for the necks were purchased from Penberthy Lumber Company in Los Angeles; but the rosewood for the fretboards, as well as the bridges, tailpieces and tremolos, were imported from C.A. Gotz in Germany. Other hardware, as well as the electronics, Luson Deluxe machine tuning heads, and strings were U.S. made and purchased locally. Victoria Luggage company in Los Angeles supplied the guitar cases.
While 1965 dragged on with research and development, Pat Murphy and Rick Geiger had a falling out, which resulted in Geiger suddenly leaving Murphy Music Industries. Murphy had to very quickly pick-up where Rick left off and begin production as soon as possible. A lot of money had already been invested without a finished product being produced.
Production finally began with a moderate team of workers and family. Initially, there were several main shop woodworkers; 3 in the paint booth, who also doubled as sanders; 4 in the final assembly section; (including Pat's eldest son, Mike Murphy), a couple of office workers of which one was Mary Jane, Pat's wife and a salesman. At the peak of production, there were as many as 22 people working at Murphy Music Industries. The company was able to produce guitars in lots of 10 at a time; and in good weeks occasionally twice that number were produced.
Originally the guitar was to be called 'York', but a brass instrument maker of the same name already existed in Grand Rapids, Michigan. So, by shortening his own surname, Pat settled on 'Murph', a one syllable name that wasn't difficult to remember.
Murphy kids with Murph Guitars.
Back Row Left to Right: Noreen, Tim, Patty
Front Row: Terry Murphy
During the latter half of 1965 and into early 1966, rapid progress was made with single and multi-pickup, solid body guitars, and amplifiers being built. in the summer of 1966, the company went to the National Association of Music Merchants (NAMM) show in Chicago to showcase their now almost complete range of products. (See our gallery page for a full list of products.) Included in Murphy's samples for the show were products in either final prototype development or in the early stages of production. Some of them were a new 'heart' shaped design, a big bodied semi-hollow model, a 'build your own guitar' kit, and an acoustic guitar. There was even a half sized, portable, 6v battery-powered toy guitar that had an amplifier which doubled as the guitar stand. During development everyone at the factory referred to it as the 'Baby Murph'. Mattel Toy Company thought it was a good idea and showed interest.
About this same time, an agreement was being negotiated with Sears to have Murphy Music Industries make guitars under Sear's brand name of Silvertone. This was thought to be a sales boom for the company. Unfortunately, Sears ended up ordering less than 25 guitars because they had already used what was left in their yearly budget for the 'Silvertone' purchases. However, Murphy Music Industries got a promise that a larger order would follow the next year.
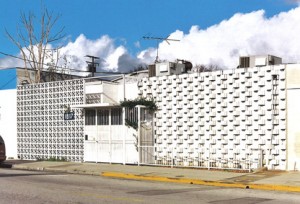
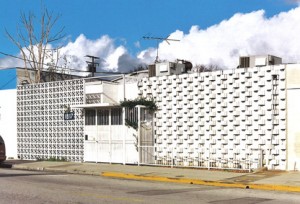
The Murph Guitar Factory
Murphy Music Industries
1817 First Street
San Fernando, California
Murphy Music Industries was like any small business trying to make a big break on a shoestring budget with high hopes and strong determination. Creating such a wide variety of models and options in just under two years (and the expense of having 22 employees) plus money being poured back into the company, along with lines of credit being stretched to the limit, was a real strain for this small California company. Unfortunately, it meant the business was about to face its biggest challenge yet.
Upon returning from the NAMM convention, Murphy Music Industries received an unexpected 'cease and desist' letter from CBS owned Fender Guitars alleging patent infringement on the design of Murphy's Squire guitars which, with their 'offset body' shape was deemed to be too much like the Jazzmaster/Jaguar. Murphy was in a dilemma - the thought of halting production for one or two years while going through litigation was more than the company could afford while proving there was no validity to the claim (compare the shapes yourself - similar but certainly no copy). To make matters worse, after receiving orders for Murph guitars on consignment, many music stores were starting to return them as pressure was being brought to bear by the bigger player.
Murphy Music Industries soldiered on into early 1967 but it was inevitable that these insurmountable pressures and the resultant lack of sales would cause the company to become insolvent. They sadly filed for bankruptcy around March/April of 1967.
After the demise of the guitar business, Pat started a mobile catering company, serving the needs of construction workers at building sites and factory workers - a world away from making guitars. This successful venture saw him through until retirement in the mid 1990s.
Our loving and generous father and grandfather passed away surrounded by his family on November, 2009. It was always with fondness that he recollected those days when he was a builder of 'Top quality American made guitars'.
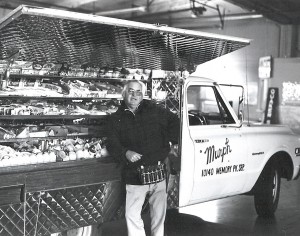
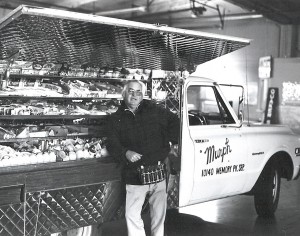
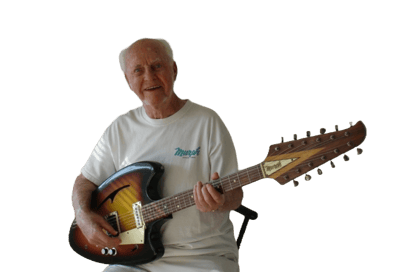
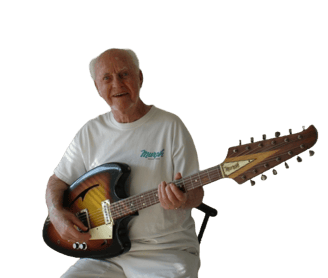